Dakar Rally Future Mission 1000: The VOSSLok40 tube forming system withstands the toughest conditions in the desert
From January 5 to 19, 2024, the “Future Mission 1000” race of the Dakar Rally took place in the desert landscape of Saudi Arabia.
Dakar Rally Future Mission 1000: The VOSSLok40 tube forming system withstands the toughest conditions in the desert
From January 5th to 19th, 2024, the "Future Mission 1000" race of the Dakar Rally took place in the desert landscape of Saudi Arabia. What makes this race unique is that only emission-free vehicles with the following drive types are allowed: fully electric, fully hydrogen-powered, and hybrid technology. With the "Future Mission 1000," a completely new format was established towards a more sustainable future. The vehicles participating in this race travel across twelve stages, each approximately 100 kilometers long. During the race, they are exposed to the toughest conditions, including rubble, sand, rocks, fine dust, as well as strong impacts and vibrations. Designers and developers are putting their innovative cutting-edge technologies for a more sustainable future to the ultimate test.
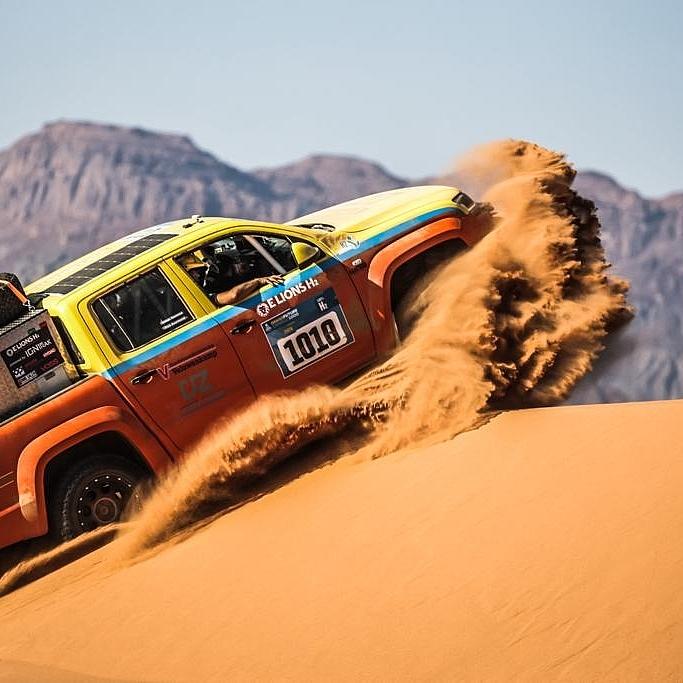
The challenge: Conversion within three months
In the ‘Future Mission 1000’, a total of ten participants competed with four hydrogen vehicles and one fuel cell vehicle. One of the vehicles was a 3.3-ton premium-class pickup, which was converted from an internal combustion engine to fuel cell. Together with our partners E-Lions H2 (specialists in converting diesel-powered commercial vehicles to fuel cell electric), E-car-tech (engineering partner for electromobility), and IONTRAK (system supplier for hydrogen systems and converter of commercial vehicles to electric drivers), we joined forces to retrofit the vehicle for the Daker Rally within three months.
To meet this challenge in such a short time, we leveraged our expertise as a trusted premium manufacturer and quality provider of connection systems for mobile and stationary hydraulics as well as hydrogen applications.
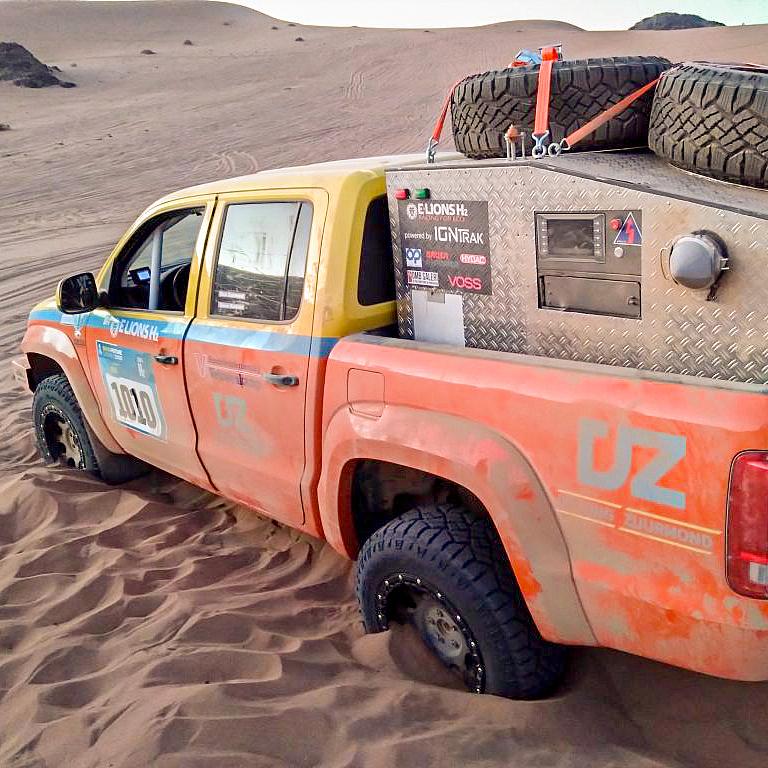
The solution: Leak-free to the finish line with VOSSLok40
Under immense time pressure, we delivered the entire custom-developed tube system, including installation-friendly connection components. These had to be suitable for both the high and low-pressure areas of the hydrogen system in the vehicle, to connect to all interfaces between the fill nozzle/receptacle and the inlet to the fuel cell. The solution was VOSSLok40, an innovative tube forming system and a cost-effective alternative to compression fittings. The stainless-steel system has been proven for years and is in serial production. In this case, it stands out especially for its high leak-tightness up to 700 bars.
To achieve this, a sealing and holding contour is formed at the tube end using a special forming machine. This ensures maximum leak protection even under extreme conditions, as required for hydrogen applications. The fitting and the tube contour are precisely coordinated to achieve the highest compression of the sealing surfaces. This process eliminates surface defects in the tube and ensures optimal sealing of potential leakage paths.
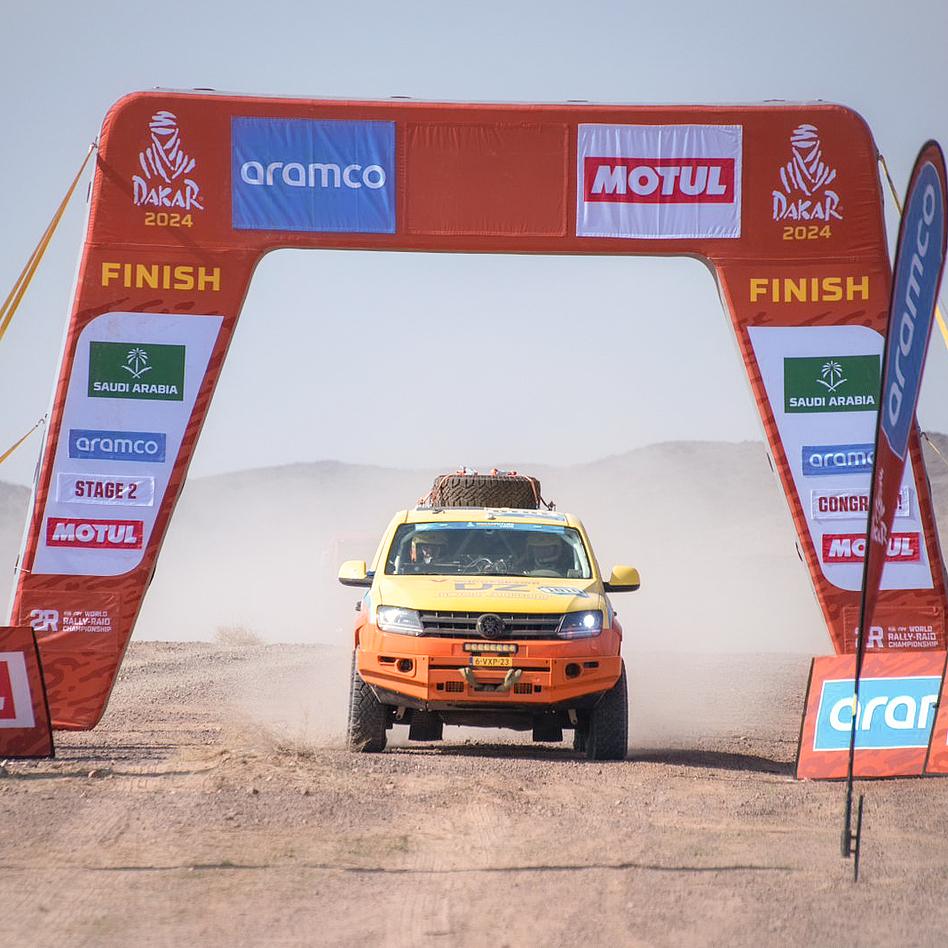
Leak-free, easy to assemble, and corrosion-resistant
The Dakar Rally is known for its challenging terrain and the extreme demands it places on both people and vehicles. Fine dust and immense forces act on the components, especially on rocky ground and at high speeds. Therefore, it was an advantage that the VOSS stainless steel components used were made of non-magnetic, corrosion-resistant austenitic chromium-nickel steel, making them ideal for this application due to their high resistance to corrosion.
Due to the tight timeline, there was no opportunity for on-site testing. Here, VOSSLok40 impressed with its simple assembly process, which could be completed in just a few steps. In addition to the use of connection components in the low-pressure area, leak-tightness and operational reliability were of utmost priority in the high-pressure areas, particularly for the hydrogen application, due to safety concerns. To monitor this and quickly locate any potential leaks, a hydrogen sensor and a sniffing method were used. The sensor continuously monitored the system, while the sniffing method was applied in advance at the individual interfaces. In the event of a leak, the sensors would have detected the medium's escape, thereby preventing further vehicle operation.
The efforts paid off: The VOSSLok40 tube forming system withstood the desert's harsh conditions! Thanks to the combined efforts of all partners, the retrofitted premium pickup reached the finish line without incidents as the fifth vehicle, with the team Stichting Rainbow Trucks and Dutch driver Dick Zuurmond.
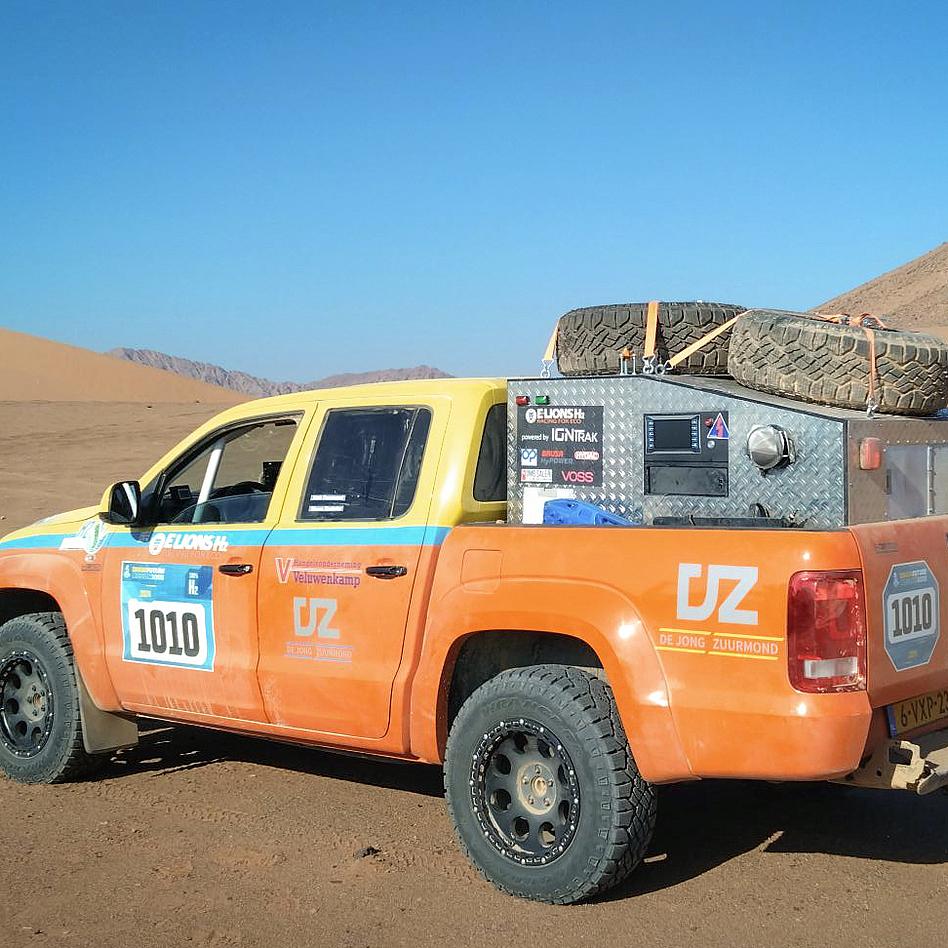
For what?
- For high leak-tightness and leak safety up to 700 bars, especially in hydrogen applications
- Corrosion resistance thanks to non-rusting chromium-nickel steel
- Connection for low to high-pressure applications
For whom?
- Designers and engineers who need a solution for harsh tests in a short time
Great, because...
- Simple and fast assembly and disassembly + ease of maintenance
- Maximum process safety during assembly
- A connection solution that guarantees maximum leak-tightness even under the most demanding conditions – for example, in hydrogen and CNG applications